Luftkreislauf-Technologie
Mirai Intex nutzt die fortschrittliche Luftkreislauftechnologie, auch bekannt als umgekehrter Brayton-Kreislauf mit Rekuperator, um effiziente und umweltfreundliche Kühllösungen zu liefern.
Der Prozess:
1. Komprimierung: Die Luft wird komprimiert, wodurch sich ihr Druck und ihre Temperatur erhöhen.
2. Wärmeaustausch: Die komprimierte Luft wird in einem wassergekühlten Wärmetauscher abgekühlt.
3. Rekuperation: Die Luft wird in einem Rekuperator durch Wärmetausch mit der Abluft weiter abgekühlt.
4. Expansion: Die abgekühlte Luft wird in einem Turboexpander entspannt, wodurch ihre Temperatur drastisch gesenkt wird. Diese kalte Luft wird dann entweder zur Kühlung einer Kammer (bei Maschinen mit offenem Kreislauf) oder einer Wärmeträgerflüssigkeit (bei X Cryo und Maschinen mit geschlossenem Kreislauf) verwendet.
5. Umwälzung: Die Luft wird im Rekuperator wieder erwärmt und dann erneut verdichtet, wodurch sich der Zyklus wiederholt.
Präzise Steuerung:
Synchronmotoren mit Invertersteuerung ermöglichen es den Mirai Intex-Systemen, die Drehzahl stufenlos zu regeln, was einen optimalen Wirkungsgrad und einen präzisen Teillastbetrieb gewährleistet.
Der Prozess:
1. Komprimierung: Die Luft wird komprimiert, wodurch sich ihr Druck und ihre Temperatur erhöhen.
2. Wärmeaustausch: Die komprimierte Luft wird in einem wassergekühlten Wärmetauscher abgekühlt.
3. Rekuperation: Die Luft wird in einem Rekuperator durch Wärmetausch mit der Abluft weiter abgekühlt.
4. Expansion: Die abgekühlte Luft wird in einem Turboexpander entspannt, wodurch ihre Temperatur drastisch gesenkt wird. Diese kalte Luft wird dann entweder zur Kühlung einer Kammer (bei Maschinen mit offenem Kreislauf) oder einer Wärmeträgerflüssigkeit (bei X Cryo und Maschinen mit geschlossenem Kreislauf) verwendet.
5. Umwälzung: Die Luft wird im Rekuperator wieder erwärmt und dann erneut verdichtet, wodurch sich der Zyklus wiederholt.
Präzise Steuerung:
Synchronmotoren mit Invertersteuerung ermöglichen es den Mirai Intex-Systemen, die Drehzahl stufenlos zu regeln, was einen optimalen Wirkungsgrad und einen präzisen Teillastbetrieb gewährleistet.
Reduzierter Stromverbrauch bis zu
30%
Das Hauptmerkmal ist die Anordnung von Turboexpander und Kompressor auf derselben Welle. Die beim Expansionsprozess erzeugte Energie wird über die Welle auf den Kompressor übertragen, wodurch der Energieverbrauch im Vergleich zu Dampfkompressionssystemen um bis zu 30 % gesenkt wird.
Luftlagerung
Die Maschinen von MIRAI INTEX verwenden keine herkömmlichen Gleitlager, die geschmiert werden müssen. Stattdessen haben wir eine neue Generation von Luftlagern entwickelt. Diese Lager laufen seit Millionen von Stunden und haben ihre hohe Effizienz und Zuverlässigkeit bewiesen und gewährleisten einen minimalen Wartungsaufwand.
Der Einsatz von Luftlagern hat es uns ermöglicht, die Konstruktion des Kompressors erheblich zu vereinfachen, da kein Öl und kein Strom verbraucht wird, was den Wirkungsgrad des Kompressors erhöht und ihn vor Stromausfällen bewahrt.
Der Einsatz von Luftlagern hat es uns ermöglicht, die Konstruktion des Kompressors erheblich zu vereinfachen, da kein Öl und kein Strom verbraucht wird, was den Wirkungsgrad des Kompressors erhöht und ihn vor Stromausfällen bewahrt.
Snow Catcher
Feuchtigkeitsabsauggerät HED
Bei extrem niedrigen Temperaturen verwandelt sich Feuchtigkeit sofort in Eis. Deshalb hat Mirai Intex einen einzigartigen Feuchtigkeitsabsauggerät - Humidity Extraction Device (HED) - entwickelt, mit dem regelmäßige Abtauvorgänge der Vergangenheit angehören. Dank dieser einzigartigen Vorrichtung können die Maschinen kontinuierlich arbeiten, ohne Abtauvorgänge , die Kühlleistung und zusätzliche Energie verbrauchen.
Die Installation der Maschine ist sehr einfach - es müssen nur ein paar Löcher in die Wand des Kühlraums geschnitten werden, um den MIRAI Cold and HED anzuschließen.
Die Installation der Maschine ist sehr einfach - es müssen nur ein paar Löcher in die Wand des Kühlraums geschnitten werden, um den MIRAI Cold and HED anzuschließen.
F-Gase Reglementierungsgesetzt der europäischen Union
Das Ziel der schrittweisen Reduzierung der F-Gas-Emissionen ist es, die Verwendung von HFKW zwischen 2015 und 2030 um 95 % zu reduzieren. Wir bei Mirai unterstützen unsere Kunden mit alternativen Kältelösungen mit einem GWP NULL. Luft unterliegt nicht der F-Gas-Regulierung und ist der beste Ersatz für bestehende Kältemittel und bietet volle Kühlung, Kapazität und Sicherheit.
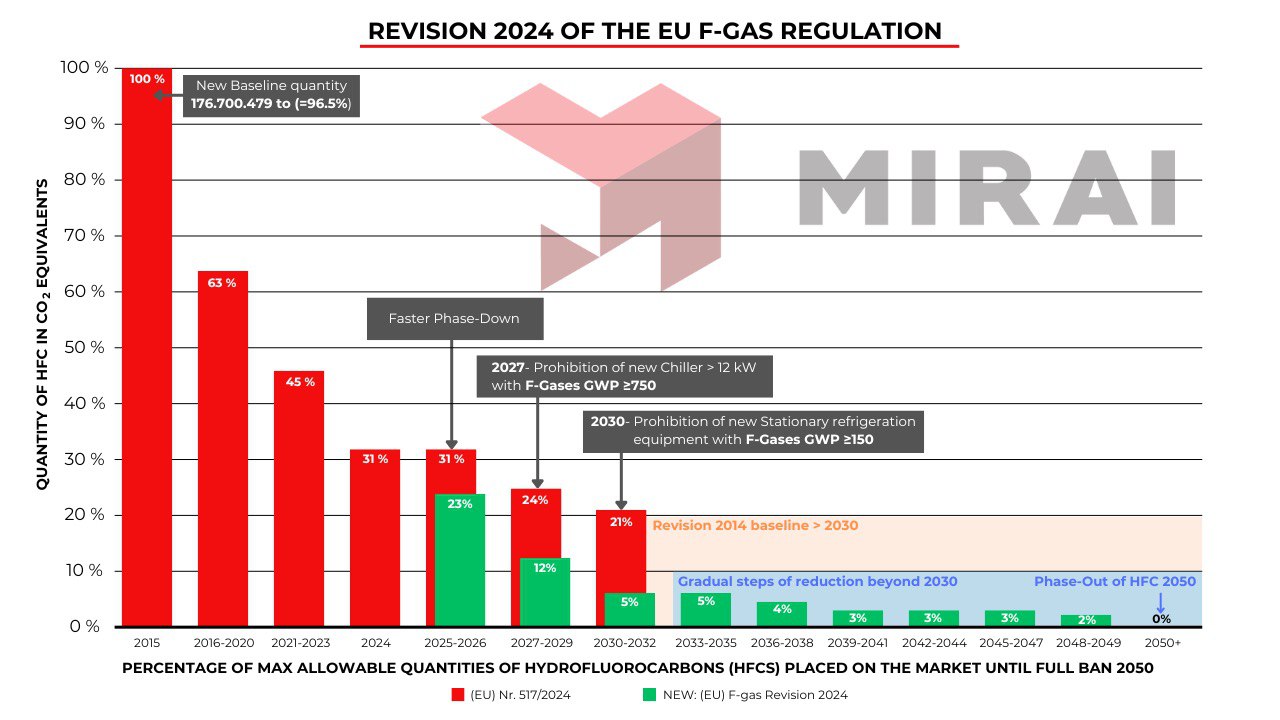
Umweltfreundlich
- Luft als Kältemittel
- Kein Nachfüllen erforderlich
- Umweltfreundlich
Ölfrei
- Kein Öl im System dank der Luftlagerung
- Geringere Kosten
Einhaltung der Gesetze
- Einhaltung der Gesetze
- Einhaltung aller internationalen Normen / Vorschriften
Stabilität des Betriebs
- Stabile Kälteleistung beim Betrieb mit Kühlwasser
Sichere Lösung
- Keine chemischen Stoffe
- Keine Brand- oder Explosionsgefahr
Keine Vibrationen und stark reduzierter Lärm
- No vibration or noise
- Das Design des Turbomoduls reduziert Lärm und Vibrationen
Kältetechnologie
Vergleichstabelle
Luftkreislauf
Kompressionskältetechnik
Flüssiger Stickstoff
Zukunftssicher
Luft als Kältemittel
Kostenloses Kältemittel
GWP = 0
Verbot synthetischer Kältemittel
Durch Sicherheitsvorschriften eingeschränkte Kältemittel
Regeln für den Transport
Vorschriften für die Lagerung
Sicherheit
Luftgelagerter Verdichter
Kein Kontakt der rotierenden Bauteile mit dem Gehäuse, minimaler Verschleiß
Verschleiß des Kompressors
Beschädigung durch flüssiges Kältemittel
Beschädigung durch unzureichende Schmierung
Keine beweglichen Teile
Hohe thermische Belastung
Sicherheit / Maschinenraum
Niedriger Systemdruck von 1 bis 10 bar
Minimale Maschinenraumanforderungen
ATEX-Richtlinie für die entsprechenden Kältemittel
Gassensoren, Ventilation
Schwingungsdämpfender Bodenbelag
Gassensoren, Ventilation
Raum für LN2-Lagerung
Wartung
Säuberung Schaltschrankfilter
Öl- und Kältemittelmanagement
Prüfung der Sicherheitsventile
Regelmäßige Dichtheitsprüfung
Es wird geschultes Personal benötigt
LN2 Nachfüllungen
Überprüfung der Ventilfunktion
Prüfung der Sicherheitsventile
Teilbelastung
Inklusive Frequenzumrichter
Drehzahlregelung des Turbo Kompressors
Je nach Systemdesign
Normalerweise Start/Stop oder Heißgas-Bypass
Dosierung basiert
Lebenszykluskosten
Fast keine Wartung erforderlich
Kein Kauf und Nachfüllen von Kältemittel
Erfordert viele Komponenten
Steigende Preise für Kältemittel
Intensive, kostspielige Wartung
Hohe langfristige Betriebskosten
Transport und Lagerung von LN2 vor Ort