Oil-free vs oil compressors: a comprehensive guide
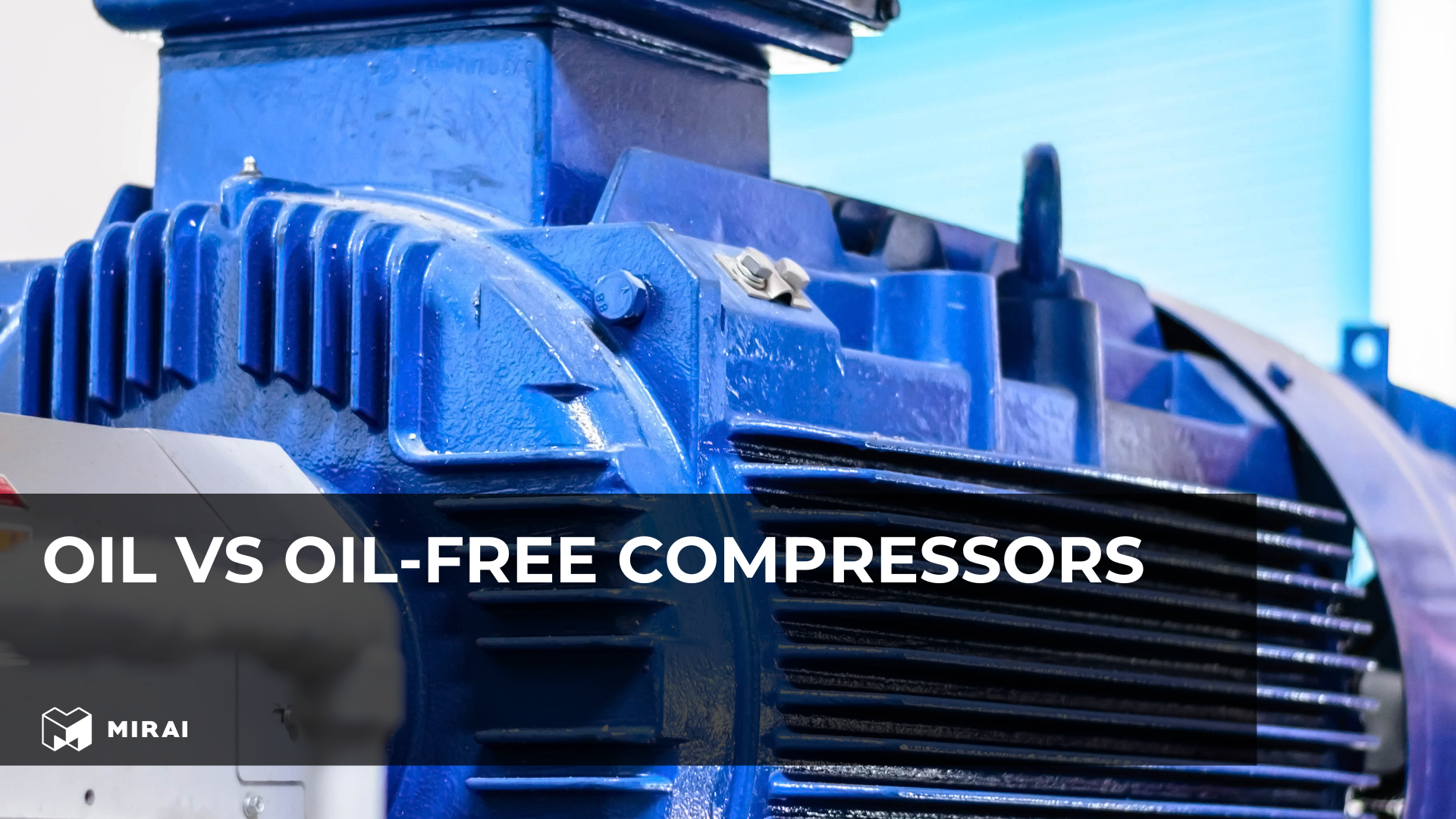
Compressors are vital components in various industries, playing a crucial role in processes that require the generation and utilization of compressed gas or air. Whether in manufacturing, automotive, or even home DIY projects, compressors are indispensable. However, the choice between oil lubricated vs oil free compressors can be daunting, as each type offers distinct advantages and disadvantages. This article will delve into the definitions, operations, and applications of both oil-free and oil compressors, providing a thorough comparison to help you make an informed decision.
Definition of a Compressor
A compressor is a mechanical device that increases the pressure of a gas by reducing its volume. The most common use of compressors is in compressing air, which can then be used to power various pneumatic tools, inflate tires, and even in refrigeration and HVAC systems. Compressors come in various types, including piston, rotary screw, scroll, and centrifugal, each with unique characteristics suited for different applications.
The Role of Oil in a Compressor
Oil plays a significant role in many types of compressors, especially in oil-lubricated or oil-injected models. The primary function of oil in a compressor is to lubricate the moving parts, such as pistons, screws, or scrolls, to reduce friction and wear. This lubrication is crucial in maintaining the efficiency and longevity of the compressor.
In oil-injected compressors, oil also serves as a coolant, helping to dissipate the heat generated during the compression process. Additionally, oil acts as a sealant, filling gaps between the moving parts and ensuring that the compressed air is effectively contained within the system. This is particularly important in rotary screw compressors, where the oil helps maintain the integrity of the compression chamber.
The Problem of Oil Contamination in Compressed Air
One of the significant drawbacks of using oil-lubricated compressors is the risk of oil contamination in the compressed gas or air. Despite the best filtration systems, traces of oil can sometimes bypass filters and mix with the compressed air. This contamination can lead to various issues, particularly in industries where clean, oil-free air is critical, such as food and beverage production, pharmaceuticals, and electronics manufacturing.
Oil contamination can damage sensitive equipment, cause product spoilage, and even pose health risks. Moreover, removing oil from the compressed air can be costly, requiring additional filtration systems and regular maintenance to ensure air quality standards are met.
The Advent of Oil-Free Compressors
The development of oil-free compressors has revolutionized industries where oil contamination is a concern. Oil-free compressors are designed to operate without the need for oil in the compression chamber, eliminating the risk of oil contamination entirely. This makes them ideal for applications requiring ultra-clean air.
Oil-free compressors typically use advanced materials and coatings on moving parts to reduce friction and wear, ensuring longevity and reliability without the need for lubrication. The advent of oil-free technology has significantly expanded the possibilities for clean, efficient, and low-maintenance solutions.
Principle of Operation
Oil Compressor
Oil compressors, also known as oil-lubricated or oil-injected compressors, operate by using oil to lubricate the moving parts inside the compression chamber. In a typical oil compressor, oil is flooded or injected into the chamber during the compression cycle. This oil helps to seal gaps, cool the system, and reduce friction between the moving parts.
Rotary screw compressors, for instance, are often oil-lubricated. The twin screws within the compressor rotate in opposite directions, compressing the air or gas trapped between them. The oil injected into the system helps maintain the seal between the screws and cools the compressed air before it exits the chamber.
Oil-Free Compressor
Oil-free compressors, on the other hand, are designed to operate without the need for oil in the compression chamber. These compressors often use alternative methods to achieve lubrication and cooling, such as advanced materials, coatings, or air-cooling systems.
For example, scroll compressors, which are commonly used in HVAC systems, utilize a stationary and a moving scroll to compress air. The scrolls are designed to operate with minimal friction, eliminating the need for oil. Similarly, some rotary screw compressors use a "dry" screw design, where the screws are coated with specialized materials to reduce friction.
Also there are different types of air-bearings in oil-free compressors, that also provides competition among oil-free compressors. The advantages and disadvantages of compressors with magnetic, ceramic and air bearings are compared.
Comparison of Oil and Oil-Free Compressors
Field of Application
Oil-lubricated compressors are commonly used in heavy-duty industrial applications where high pressure and large volumes of compressed air or gas are required. These include manufacturing plants, automotive workshops, and construction sites. The robust design and cooling capacity of oil-injected compressors make them ideal for continuous, demanding operations.
In contrast, oil-free compressors are preferred in industries where purity is paramount. This includes food and beverage production, pharmaceuticals, electronics, and medical applications. Oil-free compressors are also popular in small workshops and home use, where the demand for compressed air or gas is moderate, and air quality is essential.
Efficiency
Oil compressors are generally more efficient in terms of energy consumption, particularly in high-demand applications. The presence of oil helps to maintain a better seal and reduce heat, leading to lower energy usage during operation. However, the need for regular oil changes and filter replacements can offset some of this efficiency.
Oil-free compressors, while slightly less efficient in some cases, offer the advantage of consistent refrigerant purity and reduced maintenance costs. The absence of oil eliminates the need for oil changes and reduces the risk of downtime due to oil-related issues. Also, there are new types of oil-free compressors that can be as efficient as oil compressors, like MIRAI Intex Propane turbo-compressor .
Cost
Oil-lubricated compressors tend to be more expensive upfront due to their complex design and the need for an oil management system. However, they are often more cost-effective in the long run for high-demand applications because of their durability and efficiency.
Oil-free compressors, while typically more expensive initially, can be more economical over time, especially in applications where air or gas quality is critical. The reduced need for maintenance and the elimination of oil-related consumables contribute to lower operational costs.
Maintenance
Maintenance is a significant consideration when choosing between oil and oil-free compressors. Oil-lubricated compressors require regular oil changes, filter replacements, and monitoring of oil levels to ensure optimal performance. Failure to maintain these components can lead to reduced efficiency and potential damage to the compressor.
Oil-free compressors, by contrast, have fewer maintenance requirements. Since there is no oil to change or monitor, maintenance primarily involves checking and replacing filters and ensuring that the compressor is operating within its designed parameters. This makes oil-free compressors more convenient and cost-effective in the long term.
Noise
Noise levels can be an essential factor, particularly in environments where noise pollution is a concern. Oil-lubricated compressors tend to be quieter than oil-free models because the oil helps dampen the sound of the moving parts. This is particularly true for rotary screw compressors, which are known for their relatively low noise levels.
Oil-free compressors, especially portable and small models, can be noisier due to the lack of oil for sound dampening. However, advancements in design and materials have led to quieter oil-free compressors, making them suitable for indoor and residential use.
For example, MIRAI Intex propane turbo-compressor is quieter than many other oil-free compressors because of the latest air-bearing system, there is only one rotation part in the whole compressor, which leads to the minimum level of noise.
Advantages of Oil-Free Compressors
Oil-free compressors offer several advantages that make them appealing for various applications:
- Low Maintenance: With no need for oil changes and fewer moving parts, oil-free compressors are easier and less costly to maintain.
- Environmental Benefits: Oil-free compressors eliminate the environmental concerns associated with disposing of used oil and oil filters.
- Versatility: Oil-free compressors are available in various sizes and configurations, including small, portable models, making them suitable for a wide range of applications.
MIRAI Oil-Free Turbo-compressor on Propane
MIRAI Intex in May 2024 announced on the market an absolute innovation in the world of compressors. The world's first propane turbo compressor. Advanced oil-free two-stage centrifugal compressor using R290 was developed to enhance the cooling industry.
This compressor is unique in the world. It operates with natural refrigerant - propane, which is not harmful and is not subject to F-gas regulation. No harmful TFAs are formed after its use.
The compressor works with gas-dynamic bearings. MIRAI Intex has developed a new generation of gas-dynamic bearings, which have millions of operating hours, demonstrating their high efficiency and reliability. These bearings are used in propane turbo-compressor.
The use of gas-dynamic bearings has significantly simplified the design of the compressor by eliminating electrical components, which increases the efficiency of the compressor and does not expose it to power failures. In addition, gas dynamic bearings consume no energy to support their operation.
More over, the new compressor takes into account and solves common problems that occur with compressors, such as:
- Potential for surging - To address this issue, MIRAI provides a standard solution in their compressors: a bypass valve. This valve is managed by the MIRAI controller and is optional.
- Problems with electronics - In the MIRAI Intex compressor all electrical parts are installed in a separate electrical cabinet, which prevents issue of on-board electronics failure due to humid. Compressor is certified with an IP54 rating against splashes.
- Noise and vibration - Does not require balancing or calibration during standard operation. All parts of the compressor are designed to last the lifetime of the compressor. This compressor includes only one rotating part -the rotor, that rotates without friction or interaction with other components and ensures quiet operation 65 dB
- Long compressor restart time - MIRAI Intex has short compressor restart time - maximum 25 seconds
This innovative approach results in rapid, consistent compression with significantly lower energy consumption, making it an ideal choice for industries that prioritize both cost-effectiveness and sustainability. The compact, robust construction further ensures reliable performance in even the most demanding environments, establishing the MIRAI turbo-compressor as a leader in efficiency.
Development Trends
The compressor industry is continuously evolving, with trends focusing on improving efficiency, reducing environmental impact, and enhancing reliability.The great demonstration of it is MIRAI Intex propane turbo-compressor.
In oil-free compressors, the development of new materials and coatings is a key area of innovation. These advancements aim to extend the lifespan of oil-free compressors while reducing the need for maintenance.
Energy efficiency is another critical trend, with manufacturers working to design compressors that deliver more compressed air or gas for less energy. This includes the development of more efficient motors, improved compression techniques, and better integration with systems.
Conclusion
Choosing between an oil vs. oil-free air compressor depends on your specific needs, including the required air purity, maintenance preferences, and budget. Oil-lubricated compressors offer efficiency and durability for heavy-duty applications, while oil-free compressors provide clean, maintenance-free air for industries where contamination is a concern.
The ongoing advancements in compressor technology, including the trends in oil-free systems, ensure that there is a solution for every application, whether you need a compressor for industrial use or a small, portable compressor for home projects. The key is to evaluate the field of application, efficiency, cost, maintenance, and noise considerations to select the right compressor for your needs.