Turbo compressors: comprehensive guide
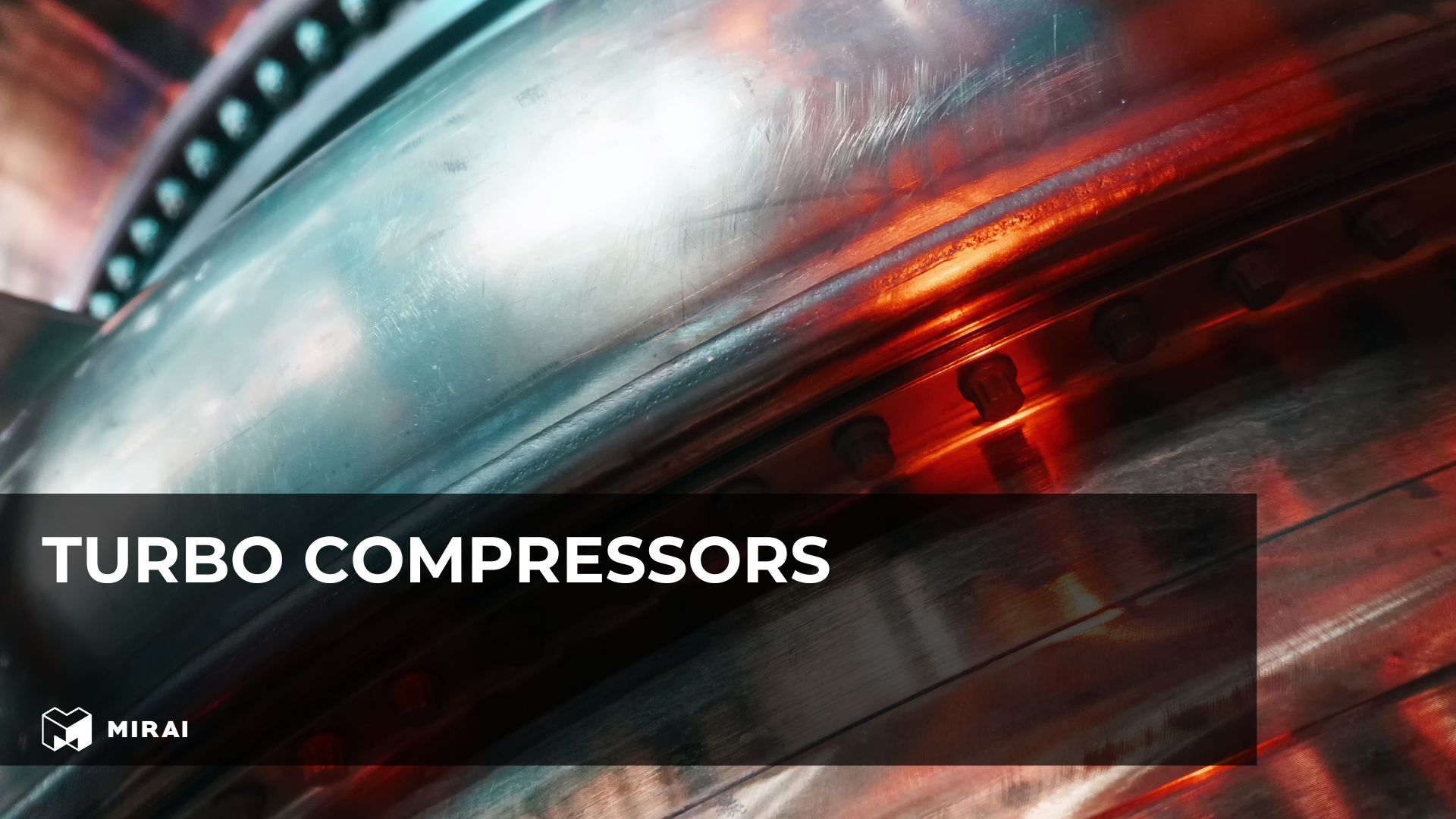
A common definition of turbo-compressor is - it is a type of dynamic compressor that utilizes a rotating impeller (or turbo wheel) to accelerate and increase the velocity of air or gas, which is then converted into pressure as the air slows down in a diffuser.
Turbo compressors are a critical component in various industrial applications, providing efficient and reliable compressed air and gas solutions. As technology advances, turbo compressors have evolved to meet the growing demands for efficiency, environmental sustainability, and performance. This article delves into the operating principles of turbo compressors, their advantages and disadvantages, and the various applications they serve. We'll also compare different types of turbo compressors, discuss criteria for selecting the right compressor, and highlight the innovative features of the MIRAI Oil-Free Turbo-compressor on Propane.
Description of the Operating Principle
A turbo compressor operates on the principle of dynamic compression, where energy is transferred from a rotating impeller, known as the turbo compressor wheel, to the gas or air being compressed. The basic components of a turbo compressor include a rotor, turbine, and housing. As the rotor spins, it imparts kinetic energy to the gas, increasing its velocity. This high-velocity gas is then decelerated in a diffuser, converting the kinetic energy into pressure energy.
In the MIRAI Oil-Free Turbo-compressor on Propane, the process is optimized through the use of advanced gas-dynamic bearings, which eliminate the need for oil lubrication and reduce friction, resulting in highly efficient compression with minimal energy consumption. The use of R290 (propane) as a refrigerant further enhances the efficiency and environmental sustainability of the compressor, making it a groundbreaking solution in the cooling industry.
Advantages of Turbo Compressors
Turbo compressors offer several advantages over other types of compressors,what makes them a preferred choice in many industrial applications:
- High Efficiency: Turbo compressors are known for their high efficiency, particularly in large-scale industrial applications. The dynamic compression process allows for the generation of high-pressure air or gas with relatively low energy input.
- Compact Design: The compact and robust design of turbo compressors makes them suitable for environments with space constraints. Despite their small footprint, they deliver powerful performance.
- Oil-Free Operation: Many modern turbo compressors, such as the MIRAI Oil-Free Turbo-compressor, operate without the need for oil. This eliminates the risk of oil contamination in the compressed air or gas, which is crucial in industries like food and beverage production, pharmaceuticals, and electronics manufacturing.Also they are quite popular in HVAC systems.
- Low Maintenance: The simplified design, particularly in oil-free models, reduces the need for regular maintenance. With fewer moving parts, the likelihood of wear and tear is minimized, leading to longer service intervals and lower maintenance costs.
- Quiet Operation: Turbo compressors are generally quieter than other compressor types, making them suitable for use in noise-sensitive environments. The MIRAI compressor, for instance, operates at a noise level of just 65 dB, thanks to its innovative design with only one rotating part.
- Environmental Benefits: The use of natural refrigerants like propane in some turbo compressors reduces the environmental impact, as these substances are not subject to F-gas regulations and do not contribute to harmful emissions.
Disadvantages of Turbo Compressors
While turbo compressors offer numerous benefits, they also have some disadvantages that should be considered:
- High Initial Cost: Turbo compressors can be more expensive upfront compared to other types of compressors. The advanced technology and materials used in their construction contribute to the higher cost.
- Complexity: The precision and engineering required to manufacture and maintain turbo compressors can make them more complex to operate and repair. This complexity may require specialized training for operators and technicians.
- Potential for Compressor Surge: Turbo compressors can be susceptible to compressor surge, a condition where the compressor cannot handle the airflow, leading to pressure fluctuations and potential damage. However, manufacturers like MIRAI Intex have addressed this issue by incorporating a bypass valve controlled by the MIRAI controller to prevent surging.
- Limited Range: Turbo compressors are typically designed for specific pressure and flow ranges, which may limit their versatility in certain applications.
Applications of Turbo Compressors
Turbo compressors are integral to a diverse array of industries, thanks to their ability to deliver high-efficiency compression for various applications. Here are some key areas where they are commonly used:
- Industrial Manufacturing: Turbo compressors provide the high-pressure air or gas needed to power pneumatic tools, drive conveyors, and operate other industrial machinery, ensuring smooth and efficient production processes.
- HVAC Systems: In both air-cooled and water-cooled chillers, turbo compressors play a critical role by compressing refrigerants like propane. This compression process is essential for facilitating cooling, whether it’s cooling air in large commercial buildings or water in industrial cooling systems. Their efficiency in these applications helps maintain optimal temperature control and energy efficiency.
- Energy Sector: Turbo compressors are vital in the energy industry, particularly in gas processing and transmission. They are used to compress natural gas, enabling its transportation through pipelines over long distances. Their reliability and efficiency make them indispensable in this sector.
- Automotive Industry: Turbochargers, which incorporate turbo compressors, are used in vehicles to increase engine efficiency. By compressing air into the engine's combustion chamber, turbochargers enhance power output and fuel efficiency, making them a popular choice in modern automotive engineering.
- Chemical Processing: In chemical plants, turbo compressors are employed to handle and compress various gases, including air, hydrogen, and other reactive or inert gases. Their precise control and ability to manage high pressures make them suitable for critical applications in the chemical industry.
In each of these applications, turbo compressors offer tailored solutions that meet specific demands, whether it’s providing precise temperature control in HVAC systems or ensuring efficient energy use in industrial and automotive applications.
Comparison of Turbocharger Types
When comparing different types of turbo compressors, it's essential to consider several factors, including their working principles, performance, pressure capabilities, compressed air quality, efficiency, cost, maintenance requirements, noise levels, and applications.
Below is a table comparing different types of turbo compressors based on key criteria:
Criteria |
Centrifugal Turbo Compressor |
Axial Turbo Compressor |
Radial Turbo Compressor |
Mixed-Flow Turbo Compressor |
|
Operating Principle |
Utilizes a rotating impeller to increase the velocity of air, which is then converted to pressure in a diffuser. |
Compresses air in a straight line through a series of axial-flow blades. |
Uses a rotating impeller to direct air radially outwards, converting velocity into pressure. |
Combines axial and radial flow, directing air at an angle to achieve compression. |
|
Performance |
High performance, suitable for medium to large applications. |
High performance for large-scale applications, especially in the power generation industry. |
Moderate to high performance, ideal for compact applications. |
Versatile performance, suitable for varying pressure and flow requirements. |
|
Pressure |
Can achieve high pressure, suitable for medium to high-pressure applications |
Capable of achieving very high pressures, ideal for large industrial uses. |
Typically generates lower pressure, better suited for low to medium pressure needs. |
Can generate moderate to high pressures depending on design. |
|
Compressed Air or Gas Quality |
High-quality compressed air or gas, especially in oil-free designs. |
High-quality air or gas, often used in critical applications requiring purity. |
Provides good air or gas quality, but may require additional filtration. |
Good air or gas quality, especially in hybrid designs that incorporate oil-free technology. |
|
Efficiency |
Very efficient, particularly in continuous operations. |
Extremely efficient in large-scale applications but may require more power. |
Efficient in specific applications, though efficiency may drop in non-optimal conditions. |
Balances efficiency with versatility, suitable for varying operating conditions. |
|
Cost |
Moderate to high initial cost, depending on size and application. |
High initial cost due to complex design and large scale. |
Generally lower cost, suitable for smaller or niche applications. |
Moderate cost, offering a balance between performance and affordability. |
|
Maintenance |
Low to moderate maintenance, especially in oil-free models. |
Requires regular maintenance due to the complex nature of the machine. |
Low maintenance, especially in simpler designs. |
Moderate maintenance, depending on the application and design. |
|
Noise |
Moderate noise levels can be mitigated with proper design. |
Can be noisy, especially at high speeds, and requires sound insulation. |
Generally quieter, suitable for noise-sensitive environments. |
Moderate noise levels vary based on design and application. |
|
Applications |
Widely used in HVAC, refrigeration, and industrial processes. |
Common in large power plants, aircraft engines, and large-scale industrial settings. |
Ideal for smaller applications, including automotive turbochargers and small-scale industrial processes. |
Used in applications that require a balance between axial and radial compressor characteristics, such as specialized HVAC systems. |
Criteria for Selecting a Compressor
When selecting a compressor, several criteria should be considered to ensure it meets the specific needs of the application:
- Pressure Requirements: Determine the required pressure levels for your application and choose a compressor capable of meeting those demands.
- Air or Gas Quality: Consider the importance of air quality in your process. For applications where contamination must be avoided, an oil-free turbo compressor is ideal.
- Efficiency: Evaluate the energy efficiency of the compressor. High-efficiency models, like the MIRAI Intex Propane Turbo-compressor, can reduce operational costs and energy consumption.
- Maintenance: Consider the maintenance requirements and choose a compressor with minimal maintenance needs if operational downtime is a concern.
- Noise Levels: If noise is a concern in your environment, choose a compressor with low noise levels, such as the MIRAI Intex compressor.
- Cost: Consider both the initial cost and the long-term operational costs when selecting a compressor.
- Environmental Impact: Evaluate the environmental impact of the compressor, including its refrigerant and energy consumption.
MIRAI Compressor Advantages
The MIRAI Oil-Free Turbo-compressor on Propane offers several advantages over traditional compressors:
- Oil-Free Operation: Ensures high air or gas quality by eliminating the risk of oil contamination.
- High Efficiency: Advanced gas-dynamic bearings and propane refrigerant contribute to low energy consumption and high efficiency.
- Low Maintenance: The simplified design with minimal moving parts reduces maintenance requirements.
- Quiet Operation: Operates at a noise level of just 65 dB, making it suitable for noise-sensitive environments.
- Environmental Sustainability: Uses natural refrigerant propane, which is not subject to F-gas regulations and does not contribute to harmful emissions.
Environmental Impact
Turbo compressors, particularly oil-free models like the MIRAI Intex Propane Turbo- compressor, have a lower environmental impact compared to other compressors. The use of natural refrigerants, such as propane, reduces greenhouse gas emissions and avoids the formation of harmful TFAs. Propane is a natural refrigerant and has ODP = 0 (ozone depletion potential) and low GWP ≈ 0.02 (global warming potential based on the Sixth Assessment Report adopted by the Intergovernmental Panel on the Climate Change) Additionally, the high efficiency of these compressors leads to lower energy consumption, further reducing their environmental footprint.
Development Trends
The development trends in turbo compressors are focused on improving efficiency, reducing environmental impact, and enhancing reliability. Manufacturers are increasingly start using natural refrigerants, like propane, to meet environmental regulations and reduce emissions. Advances in materials and design, such as gas-dynamic bearings, are also leading to more efficient and reliable compressors. Additionally, there is a growing emphasis on developing compact, low-maintenance compressors that can operate in various industrial applications without compromising performance.