Crystallization process
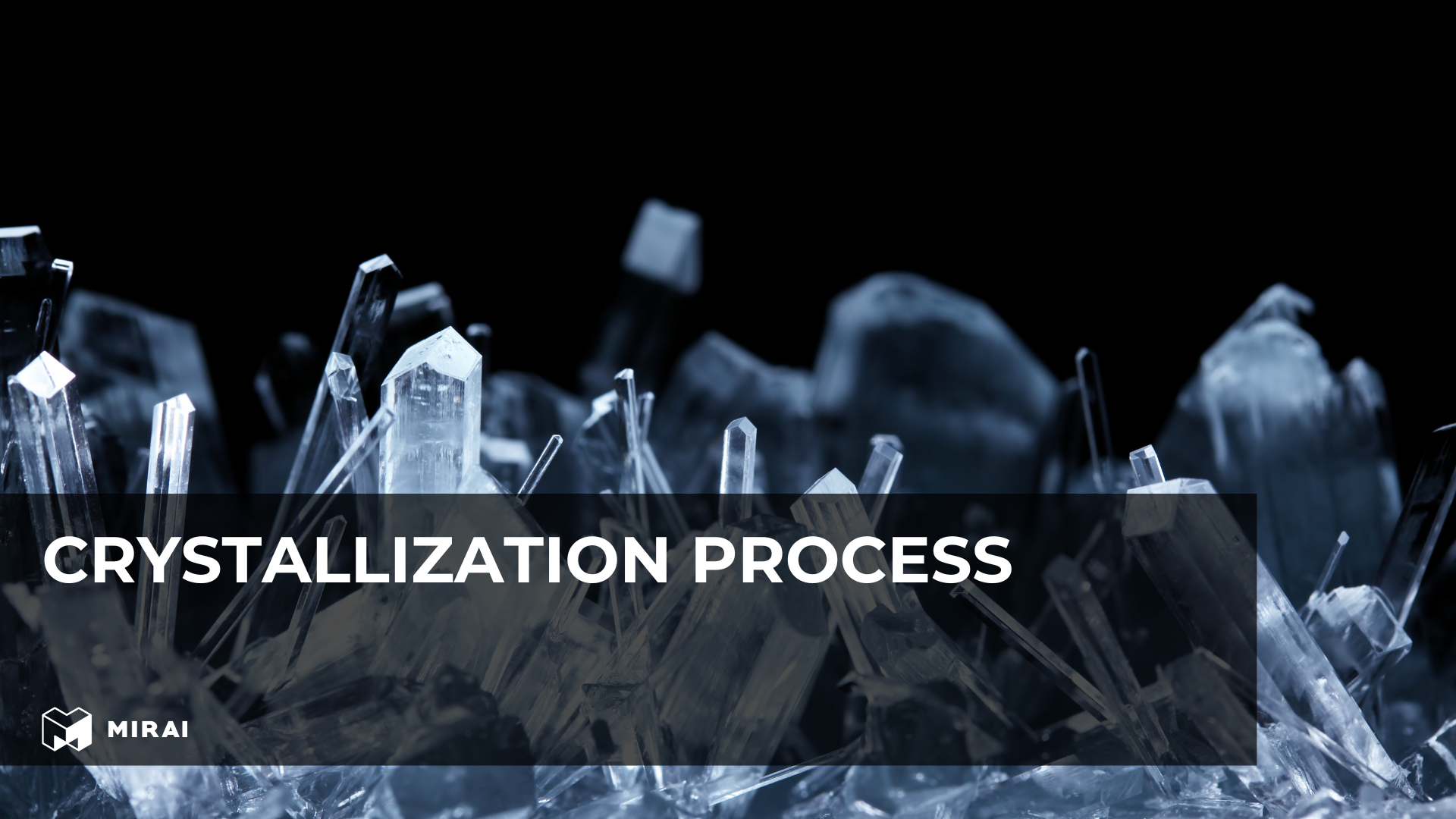
Crystallization is a vital process in many scientific and industrial applications. This article explores the crystallization definition, various crystallization methods, basic steps involved in crystallization, cooling during crystallization, its industrial uses, Mirai products that can be used in the process, and current developments and future prospects.
Definition of Crystallization
Crystallization, as defined in chemistry, is the process by which a solid forms from a liquid or gas where the atoms or molecules are highly organized into a structured pattern known as a crystal. To understand what crystallization is, one must consider the transition from a disordered state (liquid or gas) to an ordered state (solid). The crystallization meaning process involves achieving a stable thermodynamic state through this transition. This process can occur naturally or be induced artificially, and it is influenced by factors such as temperature, concentration, and the presence of impurities.
Crystallization Methods
Several techniques can be used to achieve crystallization, each with its unique applications and advantages. The primary crystallization methods include:
- Cooling Crystallization: This method involves cooling a solution to lower the solubility of the solute, causing it to crystallize out of the solution. Cooling and crystallization are closely linked in this technique, as the temperature drop is the main factor driving the process.
- Evaporative Crystallization: By evaporating the solvent, the concentration of the solute increases until it reaches supersaturation and begins to form crystals. This method is commonly used in the production of salts and other solid compounds.
- Reactive Crystallization: In this method, a chemical reaction occurs, and the product of this reaction is less soluble in the solvent than the reactants, causing it to crystallize out of the solution. This technique is frequently used in the pharmaceutical industry.
- Precipitative Crystallization: Similar to reactive crystallization, but involves adding a precipitant that induces crystallization. This method is often used for purifying substances or recovering valuable components from a mixture.
Each method is selected based on the chemical properties of the substances involved and the desired characteristics of the final crystals.
Basic Crystallization Steps
The crystallization process can be broken down into several basic steps, each crucial for forming high-quality crystals:
- Nucleation: This is the initial step where solute molecules in the solution begin to gather into clusters, forming tiny, stable nuclei. These nuclei serve as the foundation for further crystal growth. Nucleation can be spontaneous or induced by adding a seed crystal.
- Growth: During this stage, additional molecules continue to attach to the nuclei, causing the crystals to grow. The conditions under which growth occurs, such as temperature and concentration, must be carefully controlled to ensure uniformity and purity.
- Maturation: In the final stage, the crystals grow to their full size and reach their final shape. Proper control of environmental conditions is essential to avoid defects and achieve the desired crystal quality.
Cooling During Crystallization
Cooling is a critical factor in the crystallization process. The rate at which a solution is cooled can significantly affect the size, purity, and quality of the crystals formed. This relationship between cooling and crystallization is vital for achieving optimal results, particularly when working with extremely low temperatures of -40°C and lower.
- Slow Cooling: Slow cooling, typically at a rate of 0.1°C to 1°C per minute, allows for the gradual formation of larger and more well-formed crystals. In many industrial processes, this might involve cooling a solution from an initial temperature of 0°C down to -40°C over several hours. This method ensures that solute molecules have sufficient time to organize into a stable and orderly crystal structure, minimizing defects and inclusions within the crystals. For example, the solution could be cooled from -20°C to -40°C at a controlled, slow rate to achieve high-purity and well-defined crystals.
- Rapid Cooling: Rapid cooling, occurring at rates of 10°C per minute or faster, can result in the formation of smaller, less pure crystals. In practical applications, this might involve rapidly cooling a solution from 0°C to -40°C within a few minutes. The swift temperature drop forces solute molecules to quickly come together, often resulting in a less orderly arrangement. This method is suitable for processes where speed is critical, and the purity and size of the crystals are less important. However, the rapid formation of crystals can lead to higher levels of impurities being trapped within the crystal lattice, compromising overall quality.
- Quench Cooling: Quench cooling is an extreme method where the solution is rapidly cooled using cryogenic techniques, such as immersion in liquid nitrogen, which brings the temperature down to around -196°C almost instantaneously. This method is used to prevent the formation of any crystalline structure, resulting in an amorphous solid. Quench cooling is particularly useful in applications where the formation of crystals must be avoided, such as in the production of certain pharmaceuticals and glassy materials. The abrupt temperature change ensures that the solute molecules do not have time to arrange into a crystal lattice, thereby preserving the desired amorphous state.
- Controlled Cooling Systems: Modern controlled cooling systems allow precise management of the cooling rate, often using programmable settings to achieve desired crystallization outcomes. These systems can dynamically adjust the cooling rate based on real-time monitoring of the crystallization process, ensuring optimal conditions for crystal growth. For example, a system might start cooling a solution from 0°C at a slow rate of 0.5°C per minute until reaching -20°C, then speed up to 5°C per minute until it reaches the final temperature of -40°C. This tailored approach helps in achieving uniform crystal size and high purity.
- Temperature Gradients: Utilizing temperature gradients, where different parts of the solution are cooled at varying rates, can enhance the crystallization process. For instance, a solution could be cooled from -10°C to -40°C, with different segments experiencing cooling rates ranging from 1°C to 10°C per minute. This method helps in achieving a more uniform distribution of crystal sizes and prevents localized supersaturation, which can lead to the formation of unwanted crystal phases.
Where Crystallization is Used in Industry
Crystallization is a crucial process in various industries due to its efficiency in separating and purifying substances. Here are some examples of where crystallization is used in industry:
- Pharmaceutical Industry: Crystallization is used to purify active pharmaceutical ingredients (APIs) and produce drugs with precise dosages. The quality and efficacy of pharmaceuticals often depend on the purity and form of the crystalline compounds.
- Chemical Industry: This process is essential for producing high-purity chemicals and intermediates. Crystallization helps in separating and purifying chemical compounds from mixtures.
- Food Industry: Crystallization is used in the production of various food products, such as sugar and salt. It helps in obtaining pure and consistent crystalline products.
- Mining and Metallurgy: In these industries, crystallization is used to recover valuable minerals and metals from ores and solutions.
- Environmental Engineering: Crystallization processes are used for waste treatment and the recovery of reusable materials from waste streams.
Mirai Products That Can Be Used in the Crystallization Process
MIRAI Intex machines, known for their ability to create and maintain extremely low temperatures, can be effectively used for a variety of crystallization processes. This process finds wide application in the chemical, pharmaceutical, and food industries. In this chapter we will look at how the technologies used in MIRAI Intex machines can be applied to optimize and control crystallization processes.
It is important to maintain stable and predictable temperature conditions to obtain crystals with specific properties.
MIRAI Intex machines, capable of maintaining temperatures down to -60 °C and below, are ideal for processes requiring low-temperature crystallization. This can involve both cooling melts to the crystallization point and maintaining stable conditions throughout the process.
Applications in the chemical and pharmaceutical industries
In the chemical and pharmaceutical industries, crystallization is often used to purify and obtain substances in their crystalline form. Controlling the size and shape of the crystals can significantly influence the properties of the final product such as solubility, stability and bioavailability.
The use of MIRAI Intex machines in these industries helps to ensure process stability by preventing overheating or overcooling, which can lead to uneven crystal growth. It helps in stable temperature control, which is especially important when working with temperature-sensitive substances that can decompose at higher temperatures. In addition, these machines help in
optimizing energy efficiency, these cooling systems reduce energy costs, making the process more cost-effective.
Technological advantages of MIRAI Intex machines
MIRAI Intex machines offer a number of advantages that make them attractive for use in crystallization processes:
- High precision and stability. Precise temperature sensors and an advanced control system make it possible to achieve and maintain the required temperature conditions.
- Compactness and modularity. This allows the equipment to be easily integrated into existing production lines.
- Environmental sustainability. Mirai Intex machines use only air as refrigerant for their operation, making it the most environmentally friendly solution.
MIRAI Intex machines provide innovative solutions for controlling crystallization processes in various industries. Their ability to provide extremely low and stable temperatures makes them ideal for processes where crystallization control is critical. The use of these machines not only improves product quality, but also optimizes the economic and environmental aspects of production.
Current Developments in the Field and Future Prospects
The field of crystallization is continuously evolving, with ongoing research and development aimed at improving existing techniques and discovering new methods. Some current developments and future prospects include:
- Advanced Crystallization Technologies: Innovations such as ultrasound-assisted crystallization and microwave-assisted crystallization are being explored to enhance nucleation and growth rates, resulting in higher quality crystals.
- Sustainable Crystallization Processes: Researchers are focusing on developing environmentally friendly crystallization methods that reduce energy consumption and minimize waste.
- Nano-Crystallization: The study of nano-sized crystals and their unique properties is opening up new possibilities in materials science and pharmaceuticals.
- Automation and Control: Advances in automation and process control are enabling more precise and efficient crystallization processes, reducing the need for manual intervention and improving reproducibility.
- Hybrid Techniques: Combining different crystallization methods to leverage their respective advantages is a promising area of research. For example, combining cooling and evaporative crystallization to optimize crystal formation.
In conclusion, crystallization is a fundamental process with a wide range of applications in science and industry. Understanding the crystallization definition, methods, and steps involved, as well as the importance of cooling during crystallization, is essential for optimizing this process. With ongoing advancements and innovative products from companies like Mirai, the future of crystallization looks promising, offering improved efficiency, sustainability, and quality in various industrial applications.