Oil free compressor pump
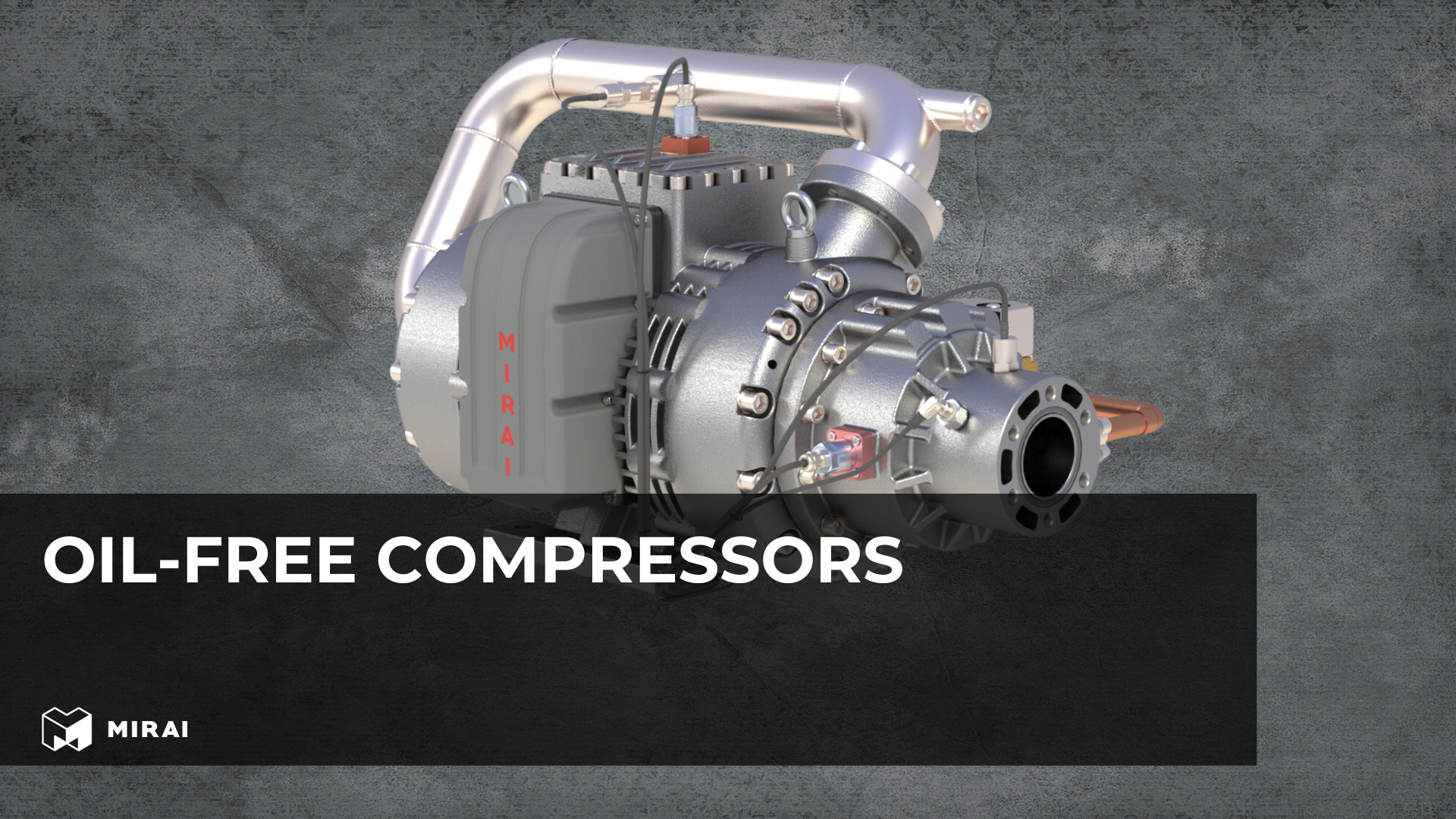
An oil-free air compressor is a machine that compresses air without the need for lubricating oil in the compression chamber. Unlike traditional air compressors that rely on oil to lubricate the moving parts, oil-free air compressors utilize alternative technologies to ensure smooth operation and longevity. This makes them an ideal choice for applications where clean air is paramount.
These compressors work by using an oil-free air compressor pump, which eliminates the need for oil lubrication. This results in cleaner air output, as there is no risk of oil contamination. The oil-free air compressor motor is designed to function efficiently without the need for oil, further enhancing the machine's reliability and performance.
Advantages of oil-free air compressors
Environmental friendliness
One of the main advantages of oil-free air compressors is that they are more environmentally friendly. By eliminating the need for oil, these compressors reduce the risk of oil spills and contamination, which can be harmful to the environment. They also produce less waste and require fewer resources for maintenance, making them an eco-friendly choice for many industries. But unfortunately this does not make them completely environmentally friendly, as many compressors use HFO (Hydrofluoroolefins) refrigerants to run the compressors, which when exposed to ultraviolet light will break down into harmful TFA (Trifluoroacetic Acid), which seeps into soil and water. In addition, they are expensive to use and are not suitable for all applications.
No power degradation
Oil-free compressors are renowned for the fact that they have no degradation in chiller performance over time due to the absence of oil, as oil does not contaminate the system. In addition, the graph below clearly shows that natural refrigerants such as propane can be much more efficient than natural refrigerants such as oil.
Applications
Oil-free air compressors are used in a wide range of applications due to their ability to provide clean and reliable air. Some common uses include:
- Food and Beverage Industry: Ensuring that the air used in production processes is free from oil contamination.
- Pharmaceutical Industry: Maintaining sterile environments by providing clean air.
- Electronics Manufacturing: Preventing oil contamination in sensitive electronic components.
- Medical Field: Providing clean air for respiratory devices and other medical equipment.
Types of Oil-free compressors
Oil-free compressors are essential in many industries due to their ability to provide clean, contaminant-free air. Here are the primary types of oil-free compressors, their advantages, and disadvantages:
1. Screw Compressors
Description:
Oil-free screw compressors use a rotary mechanism to compress air. They consist of two rotors that rotate in opposite directions, trapping and compressing the air between them.
Advantages:
- Highly efficient and reliable.
- Suitable for continuous operation.
- Low maintenance requirements.
- Durable and capable of handling high demand.
Disadvantages:
- Higher initial cost compared to other types.
- Noise levels can be relatively high.
- Requires sophisticated controls and monitoring systems.
Applications:
- Industrial applications.
- Manufacturing processes.
- Food and beverage industry.
- Pharmaceutical production.
2. Piston Compressors
Description:
Oil-free piston compressors utilize a reciprocating piston mechanism to compress air. As the piston moves up and down, it draws in air and compresses it in a cylinder.
Advantages:
- Ideal for high-pressure output.
- Versatile and portable.
- Suitable for intermittent use.
- Cost-effective for smaller-scale applications.
Disadvantages:
- Higher maintenance requirements due to many moving parts.
- Can be noisy during operation.
- Less efficient than screw and centrifugal compressors for continuous use.
Applications:
- Smaller-scale industrial settings.
- Dental and medical equipment.
- Laboratories.
- Workshop tools and equipment.
3. Centrifugal Compressors
Description:
Centrifugal compressors employ a rotating impeller to increase the velocity of air, which is then converted into pressure as the air slows down in a diffuser.
Advantages:
- High efficiency.
- Capable of continuous operation.
- Suitable for large-scale applications.
- Provides high volumes of air.
Disadvantages:
- - High initial cost and installation complexity.
- - Requires precise control and maintenance.
- - Not suitable for low airflow applications.
Applications:
- Large-scale industrial processes.
- Chemical and petrochemical industries.
- HVAC systems.
- Power generation plants.
4. Turbo-compressors
Description:
Turbo-compressors are a subset of centrifugal compressors that use high-speed turbines to compress air. They are designed for high efficiency and performance.
Advantages:
- Extremely efficient.
- Capable of providing large amounts of compressed air.
- Ideal for continuous operation.
- Low maintenance due to fewer moving parts.
Disadvantages:
- Very high initial cost.
- Requires specialized maintenance and operation.
- Sensitive to changes in operational conditions.
Applications:
- Industrial settings with high air demand.
- Aerospace industry.
- Large manufacturing facilities.
- Gas and oil refining processes.
Choosing the Right Oil-Free Compressor
Selecting the appropriate oil-free compressor depends on several factors, including the specific requirements of the application, the volume of air needed, and the desired pressure levels. Considerations should include:
- Application needs: Determine the specific requirements for air purity, pressure, and volume.
- Operational environment: Assess whether the compressor will be used in a continuous or intermittent setting.
- Maintenance and durability: Evaluate the maintenance needs and durability of the compressor type.
- Cost: Consider the initial investment and operational costs, including energy efficiency.
Recommendations for use
When selecting an oil-free compressor, it is important to consider the specific requirements of your application. Factors such as the required air pressure, volume, and duty cycle should be taken into account. Additionally, it is essential to choose a compressor from reputable oil-free compressor manufacturers to ensure reliability and performance.
Regular maintenance is also crucial to ensure the longevity and efficiency of your oil-free compressor. This includes checking and replacing parts as needed, as well as ensuring that the compressor is operating within its specified parameters.
Mirai products
Mirai recently announced its revolutionary development in the world of compressors. The world's first propane turbo compressor.
It's not just an oil-free compressor, it utilizes a promising refrigerant - propane - that is not subject to F-gas regulation.
It's the world's first propane turbo compressor. It is characterized by its reliability because it uses a new generation of air bearings that do not wear out during operation. In addition, the bearings ensure stable compressor operation without vibration noise because the rotor is the only moving part in the compressor during operation.
This compressor shows high efficiency at partial load and its structure is designed to be as convenient as possible to allow easy access to the sensors when needed. It is also equipped with remote monitoring and various options for customer convenience.
The compressor has a life cycle of 20 years.
Conclusion
Oil-free compressors are an excellent choice for many applications, offering numerous benefits such as environmental friendliness, clean air output, and reliable performance. By understanding the different types of oil-free compressors and their applications, you can make an informed decision about which compressor is best suited to your needs. Whether you require a small, portable compressor or a large industrial unit, oil-free air compressors provide a versatile and effective solution for clean, reliable air compression.