Refrigeration challenges in the Freeze-drying process and how to approach them
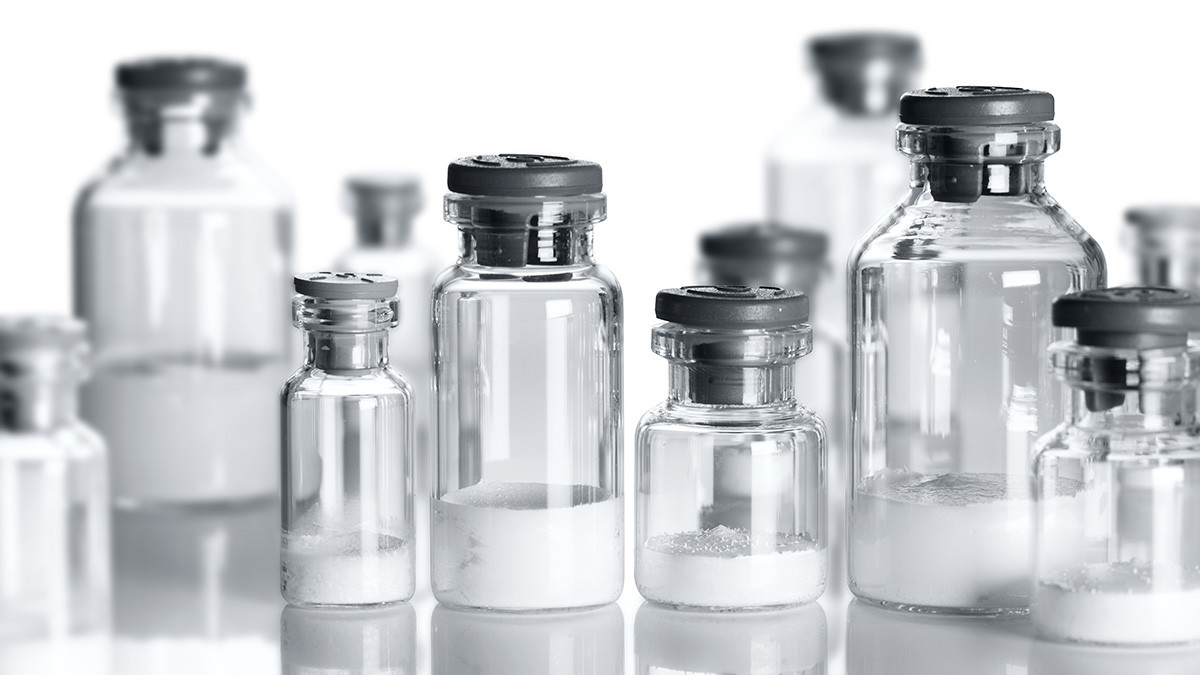
Freeze-Drying (also known as lyophilization) is a low-temperature dehydration process. Most dehydration methods use heat to remove the water by evaporation. Which makes the biggest difference when the product is re-hydrated. If the product cannot be easily re-hydrated it is considered to be of lower quality. Since the final freeze-dried product is porous complete re-hydration is possible compared to heat-based dehydration. Also, the original shape of the product is maintained. That is why freeze-drying is not only frequent in the pharmaceutical and food processing industry but in taxidermy and historical objects preservation as well.
Freeze-Drying is a delicate process that has to be controlled thoroughly to achieve the required product quality. There are four stages in the complete freeze-drying process:
- Pretreatment - product preparation prior to the freezing
- Freezing / Annealing - the product is cooled to a triple point. This is very important to ensure sublimation in the next steps, not melting. Large ice crystals are preferred. (temperature -50 ° C to -80 ° C)
- Primary Drying - Pressure decreases and heat is supplied to the product to sublimate the ice. About 95 % of the water in the material is removed.
- Secondary Drying - The remaining unfrozen water is removed. Some products require a pressure reduction, but some may benefit from increasing pressure at this stage. The final residual water content of the product is between 1 % and 4 %.
Refrigeration System for Freeze-Drying
The refrigeration industry is facing a challenge with the F-Gas Regulation; thus, freeze-drying is no exception since the refrigeration system is the key to the whole process. Lyophilization requires temperatures in the Ultra-Low Temperature (ULT) range (usually -50 °C down to -90 °C) and the cold condenser even in the sub-ULT range (usually below -90°C down to -160 °C), hence only a few options for refrigerants used in the vapor-compression systems are possible: R23 with GWP100 = 14800 and R404A. These refrigerants are neither ecological nor economical. The second option is liquid nitrogen. Unbeatable in the cryo-temperature range (usually below -160 °C) but requires high energy demand in the ULT range.
This is where the Freeze-Drying industry comes to a crossroads. To design and reliably run a large cascade system for the ULT range could be sometimes very challenging task.
The basics of the air cycle technology are very simple. With the repetition of compression end, expansion air can reach the ULT and sub-ULT temperatures. Mirai Intex has developed a new machine – MIRAI Cold. This particular application requires a version for closed-cycle operation. In the case of a closed cycle machine, the ultra-cold air is circulating only inside the refrigeration machine in a closed loop. For that reason, closed-cycle machines have to be equipped with an additional heat exchanger for the silicone oil. As a result, two closed loops interacting in the additional heat exchanger inside the refrigeration machine. The primary loop operates with the Air and the secondary loop is operating with silicone oil. MIRAI Cold was specifically designed to eliminate as many problematic points as possible.
Large-scale Freeze-Dryers come with a great benefit in the form or an external refrigeration system that usually cools down the silicone oil used to flow through the system when the product is being frozen. Therefore, not only new freeze-dryers have the opportunity to be equipped with the Air Cycle Technology refrigeration system, but also older models can be retrofitted. This all is managed very easily since MIRAI Cold is plug & play refrigeration solution.
Benefits: nutrients are preserved, shelf life is increased, effective re-hydration, easy storage and transport, production of tablets or wafers, API (Active Pharmaceutical Ingredients) preparation, best quality instant coffee, and many more.
Freeze-Dryers are very sophisticated machines being able to produce the most premium products available in the pharmaceutical, food processing, and many other industries. And now there is a chance to do it economically and ecologically with us due to the revolutionary refrigeration solution using the Air Cycle. We are Mirai Intex and you can save the planet with us.