Chemical industry cooling equipment
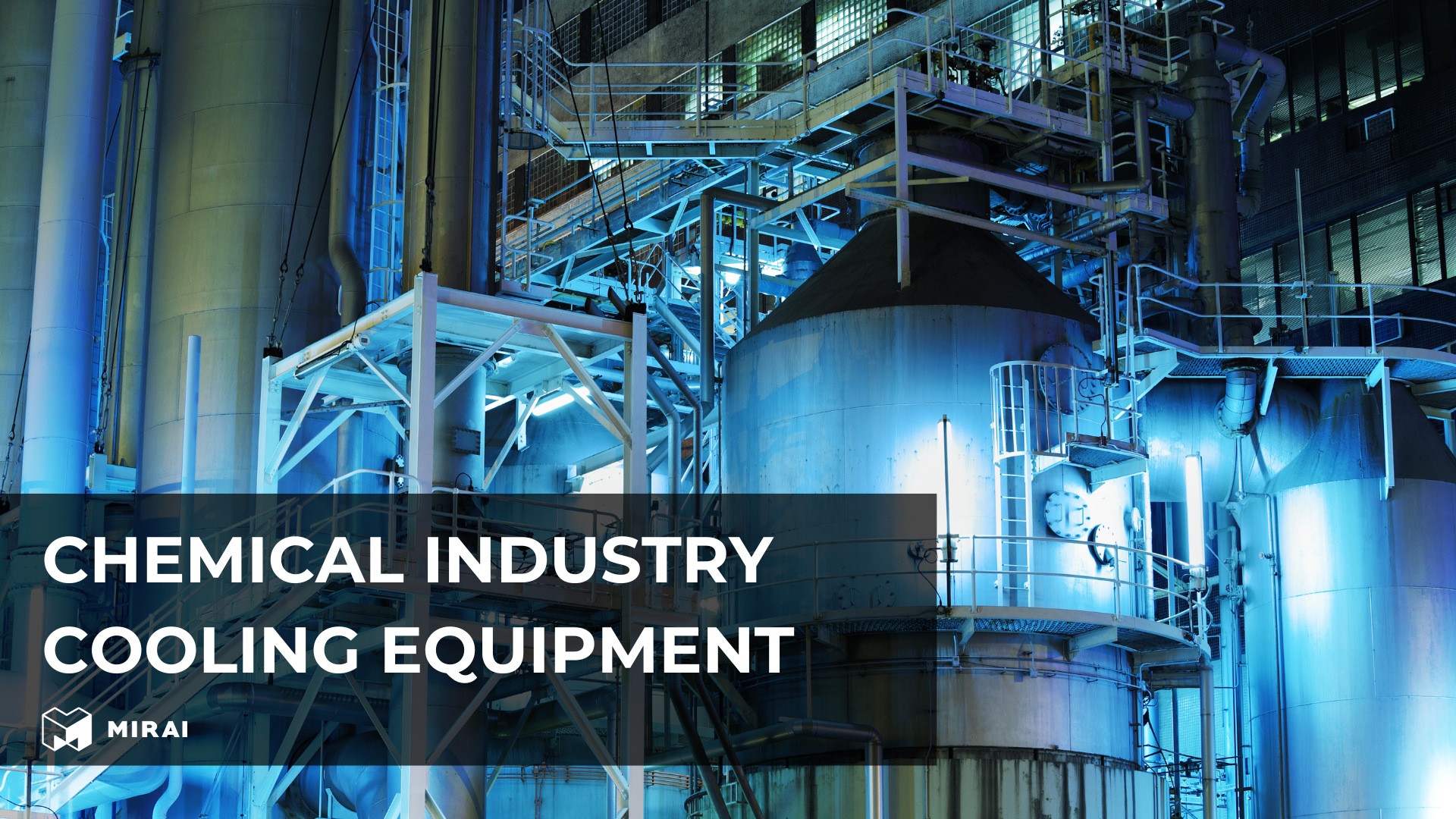
The chemical industry is an essential sector that significantly contributes to modern society, providing everything from pharmaceuticals to plastics. One critical aspect that ensures the efficiency and safety of chemical production processes is the cooling equipment used.
Relevance of refrigeration in the chemical industry
Refrigeration plays a key role in maintaining optimum conditions for organic chemistry processes. It is necessary to control exothermic reactions, to ensure stability and selectivity of sensitive compounds, and to efficiently carry out condensation and evaporation processes. Low and ultra-low temperatures (-45°C to -100°C) are often required for reactions with organometallic compounds and other sensitive materials. Effective industrial process cooling ensures that these processes run smoothly and safely, maintaining the necessary temperature control for various chemical reactions.
Cooling is also essential for condensation and evaporation processes, vital in the production and purification of many chemical compounds. Without proper cooling, these processes would be inefficient, leading to higher energy consumption and costs. Furthermore, maintaining low temperatures is critical for the storage and transportation of certain chemicals that may be sensitive to heat.
Main functions of cooling equipment in the chemical industry
Heat removal
One of the primary functions of cooling equipment is heat removal. During chemical reactions, particularly exothermic reactions, a significant amount of heat is generated. This heat must be effectively removed to prevent the temperature from rising to dangerous levels. Heat exchangers, chillers, and other cooling systems play a pivotal role in extracting and dissipating this excess heat, ensuring the process remains within the desired temperature range.
Temperature maintenance
Maintaining a consistent temperature is crucial for the stability and efficiency of chemical processes. Fluctuations in temperature can lead to inconsistent product quality and potential safety issues. Cooling equipment such as refrigeration units and cooling towers helps maintain a stable temperature by continuously regulating the heat levels within the system. This ensures that the chemical processes are conducted under optimal conditions, leading to better yields and safer operations.
Types of equipment
Air and Water Heat Exchangers
Heat exchangers are vital components in industrial cooling systems technology. They facilitate the transfer of heat between two fluids, typically air and water, without mixing them. Air heat exchangers use fans to move air across a finned surface, while water heat exchangers utilize water to absorb and carry away heat. Both types are essential for efficient heat removal and temperature control in various chemical processes.
Refrigeration units
Refrigeration units are specialized cooling systems designed to provide precise temperature control. They use refrigerants to absorb heat from the chemical process and dissipate it elsewhere, often using a combination of compressors, condensers, and evaporators. These units are highly effective for maintaining low temperatures, critical for certain reactions and storage requirements in the chemical industry.
Cooling towers
Cooling towers are large, open-topped structures that use the evaporation of water to remove heat from industrial processes. Water is pumped to the top of the tower and allowed to trickle down, where it is cooled by air flowing through the tower. The cooled water is then recirculated back into the system. Cooling towers are highly effective for large-scale cooling needs and are commonly used in factories and chemical plants.
Which MIRAI Intex equipment can be used
MIRAI Intex refrigeration machines are designed to operate efficiently at ultra-low temperatures, often required in the chemical industry. These machines can maintain stable temperatures ranging from -40°C to -130°C, making them ideal for processes involving sensitive organic and organometallic compounds, which need precise temperature control to ensure reaction stability and selectivity.
Mirai Intex offers a range of equipment suitable for industrial process cooling in the chemical industry like closed cycle machines that operate in the closed loop, with clients process.
MIRAI Intex machines utilize advanced air-cycle refrigeration technology, which provides high cooling efficiency and reliability. This technology ensures that the refrigeration units can quickly reach and maintain the desired temperatures, even in large-scale industrial applications. The high cooling capacity of MIRAI Intex machines makes them suitable for use in processes that generate significant amounts of heat.
In chemical processes, maintaining consistent temperatures is crucial to prevent hazardous situations such as thermal runaways or equipment failure. MIRAI Intex refrigeration machines are equipped with precise temperature control systems that ensure stable operating conditions, enhancing safety and reliability in chemical production.
Eco-Friendly Refrigerants
MIRAI Intex machines use environmentally friendly refrigerants,such as air, which minimize the ecological impact compared to traditional refrigeration systems. This aligns with the growing emphasis on sustainability in the chemical industry, helping companies reduce their carbon footprint.
MIRAI Intex refrigeration machines offer a comprehensive solution for the chemical industry, combining ultra-low temperature capabilities, high efficiency, safety, and sustainability.
Benefits of using quality cooling equipment in chemical industry
Investing in high-quality cooling equipment brings numerous benefits to the chemical industry:
- Energy Efficiency: Modern cooling systems are designed to be energy-efficient, reducing operational costs and minimizing environmental impact.
- Sustainability: Quality equipment often incorporates eco-friendly technologies that promote sustainability, such as water treatment systems that reduce water consumption and waste.
- Safety: Reliable cooling systems ensure safe operation by preventing overheating and maintaining stable temperatures, reducing the risk of accidents.
- Improved Product Quality: Consistent temperature control leads to better product quality and higher yields.
- Reduced Maintenance: High-quality equipment tends to be more durable and require less maintenance, leading to lower long-term costs.
Industry Trends and Innovations
The chemical industry is continuously evolving, with new trends and innovations emerging in the field of cooling equipment. Some of the latest advancements include:
- Smart Cooling Systems: Incorporating IoT and AI technologies for real-time monitoring and control, allowing for predictive maintenance and optimized performance.
- Energy Recovery Systems: Innovations in energy recovery are enabling chemical plants to harness waste heat and convert it into usable energy, improving overall efficiency.
- Advanced Materials: The use of advanced materials in heat exchangers and cooling systems enhances durability and heat transfer efficiency, leading to better performance and longer lifespans.
- Eco-Friendly Refrigerants: The development of new, environmentally friendly refrigerants helps reduce the environmental impact of refrigeration units.
Conclusion
Cooling equipment plays a vital role in the chemical industry, ensuring the efficiency and safety of various processes. From heat removal and temperature maintenance to advanced air and water heat exchangers, refrigeration units, and cooling towers, the right cooling solutions are essential for optimal operations. Mirai's innovative equipment provides effective factory cooling solutions, promoting energy efficiency and sustainability. As industry trends continue to evolve, embracing new technologies and materials will be key to staying ahead and maintaining high standards in chemical process cooling. By investing in quality cooling equipment, chemical plants can achieve better energy efficiency, sustainability, safety, and product quality, ultimately leading to more successful and cost-effective operations.