Improvement of Strength and Impact Toughness for Cold-Worked Metals using Air cycle technology
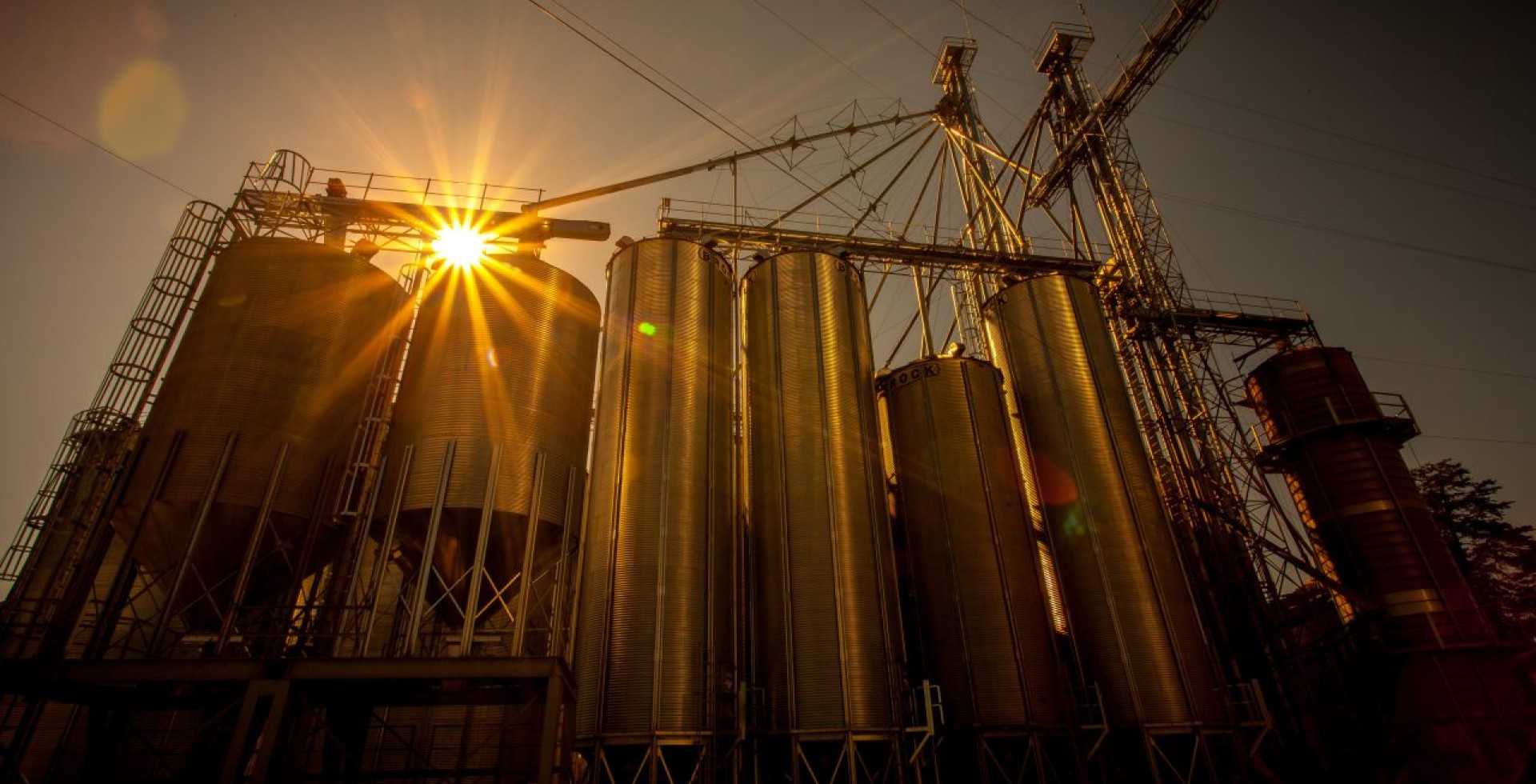
The term “cold-worked metal” refers to any metal workpiece that has been physically manipulated below the appropriate recrystallization temperature.
Traditionally, to improve metal physical properties (steel, iron, copper, and aluminum) they are often treated with heat. It undergoes a chemical reaction in which its atoms expand, while treated with heat. The heat treatment as a rule is done in conjunction with cooling.
Metal is rapidly cooled after heating to achieve more desirable properties such as increased strength and durability. Cold hardening, however, is considered a unique metalworking process in which the metal is intentionally exposed to extremely low temperatures.
A metal forming process characterized by the use of ultra-low temperatures to freeze the metal is called cold hardening. Such low temperatures increase the amount of martensite in the metal being worked, resulting in some unique benefits not available in other machining processes.
To perform cold hardening, the metal is first heated using a conventional heat treatment process, then slowly cooled. The metal is held at a stable, cold temperature for up to 24 hours, then undergoes a second heat treatment step to minimize brittleness.
Although cold hardening is a fairly complex and technical process, it provides a number of benefits, for instance, an increase in strength. As the metal’s temperature drops, its atoms are rearranged in a way that the metal’s martensite increases and its austenite decreases. Martensite is an incredibly hard crystalline structure, while austenite is soft and strong.
Metal objects and workpieces are more resistant to wear and tear due to the process of cold hardening. As a result, an increase in the service life of metal objects and workpieces is obvious.
Also, cold hardening helps relieve stress on the metal. As the metal is heated and then rapidly cooled, stresses occur. Cold hardening can eliminate and nearly remove these stresses in order to achieve a uniform homogenous composition.
This process is especially important for equipment and parts used in industries that:
- need to work in extreme conditions like in engines for the aerospace, transportation, or defense industries.
- over thousands of uses must be able to withstand repeated shocks or loads, with no loss in shape or strength, or even minor distortions.
Mirai Intex is proud to participate in new developments and contribute to new opportunities in the industrial processes. We provide our refrigeration equipment that is unparalleled, due to the use of AIR as a refrigerant is the most environmentally friendly, and easy to use.
Choose the right technologies and enjoy the process.