Solvent distillation process
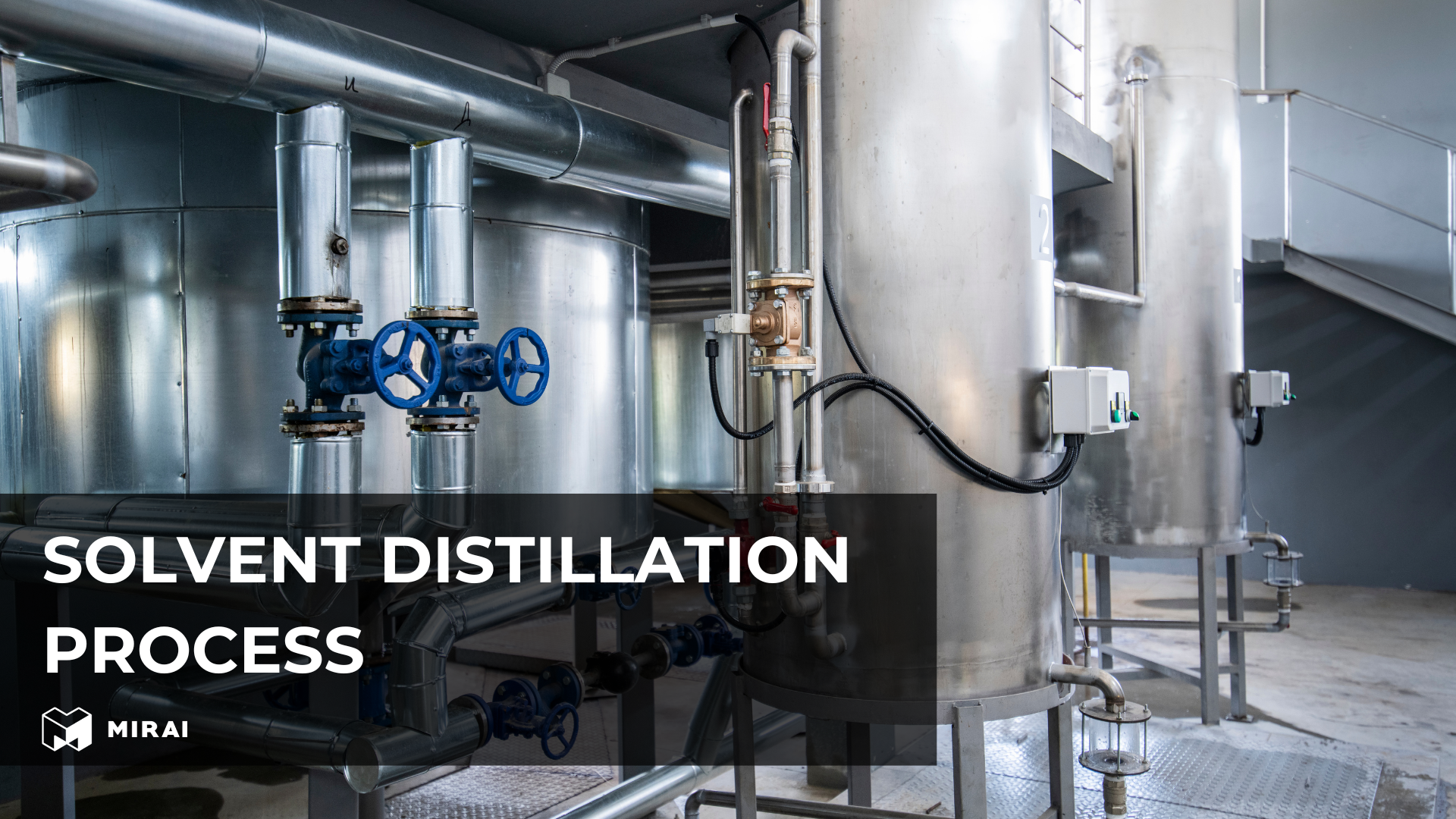
Solvent distillation is an essential method in various industries for separating and purifying chemical compounds based on their volatility differences. This article explores the definition and description of the distillation process, the types of distillation and equipment used, Mirai technologies applicable to this process, factors affecting distillation, safety considerations, the role of cold in solvent recovery, and the industries where solvent distillation is commonly- used.
Process Definition
Solvent distillation is a process used to separate a mixture of liquids into its individual components by taking advantage of the differences in their boiling points. The mixture is heated to vaporize the component with the lowest boiling point, which is then condensed back into liquid form and collected as the distillate. The less volatile components remain as the residue. This process is critical for purifying solvents, recycling used solvents, and recovering valuable compounds in industries such as pharmaceuticals, petrochemicals, and waste management.
Description of Distillation
Distillation is a physical separation technique that relies on differential boiling points. When a mixture is heated, the component with the lowest boiling point evaporates first. This vapor is then condensed in a condenser, a vital piece of equipment in the distillation system, and collected in a separate container. The effectiveness of this process depends on the volatility differences between the components, the design of the distillation apparatus, and the operational conditions.
Types of Distillation and Equipment Used in the Process
Simple Distillation
Simple distillation is the most basic form of distillation, suitable for separating liquids with significantly different boiling points. The equipment used includes a distillation flask, a heat source, a condenser, and a collection vessel. The mixture is heated in the flask, and the vaporized solvent passes through the condenser, where it is cooled and collected as the distillate. The residue remains in the distillation flask.
Fractional Distillation
Fractional distillation is used to separate mixtures of liquids with closer boiling points. It involves a more complex setup, including a fractionating column filled with packing material to increase the surface area for vapor-liquid contact. As the mixture is heated, the vapor ascends the column, condensing and re-vaporizing multiple times, enhancing the separation efficiency. This process is commonly used in the petrochemical industry to separate crude oil into its components, such as gasoline, diesel, and kerosene.
Vacuum Distillation
Vacuum distillation is employed when the boiling points of the components are too high for simple or fractional distillation. By reducing the pressure in the distillation apparatus, the boiling points of the liquids are lowered, allowing distillation to occur at lower temperatures. This method is essential for heat-sensitive compounds that might decompose at higher temperatures. Equipment used includes a vacuum pump, a distillation column, and a condenser designed to operate under reduced pressure.
Steam Distillation
Steam distillation is used for separating temperature-sensitive components, such as essential oils from plant materials. In this process, steam is passed through the mixture, causing the volatile compounds to vaporize at temperatures lower than their normal boiling points. The vapor mixture is then condensed, and the water and oil phases are separated. This method is widely used in the perfume and flavor industries.
Azeotropic Distillation
Azeotropic distillation is used to break azeotropes, which are mixtures that behave as a single substance with a constant boiling point. Special techniques, such as adding another component to create a new azeotrope with a different boiling point, are employed. This method often involves complex equipment and careful control of operational conditions to achieve effective separation and purification.
Mirai Intex Products That Can Be Used In The Distillation Process
Mirai Intex specializes in producing ultra-low temperature refrigeration machines, enhancing the efficiency and safety, that are suitable for the solvent distillation process.
Advanced equipment allows precise control over temperature, pressure, ensuring optimal solvent separation and purification.
Furthermore, their monitoring and control systems enable real-time adjustments and predictive maintenance, reducing downtime and operational costs.
In collaboration with HOF and Refolution, Mirai Intex has developed a project focused on solvent recovery through cryogenic condensation. This approach uses Mirai's refrigeration machine MC 10 CWT to cool exhaust gasses, condensing volatile components into liquid condensates for reuse, cleaning, or disposal. The system, characterized by its modular design and adjustable temperature control between -40°C and -110°C, employs natural refrigerants, enhancing both safety and environmental sustainability. This collaborative project exemplifies the successful integration of advanced cooling technology and innovative solvent recovery methods, ensuring high performance and efficiency under varying conditions.
For more details on HOF CryoProPhase technology and the collaborative project, visit Mirai references page.
Factors Affecting the Process and Safety
Several factors influence the efficiency and safety of the solvent distillation process:
Volatility
The volatility of the components in the mixture directly affects the ease of separation. Higher differences in boiling points lead to more efficient separation.
Pressure and Temperature Control
Precise control of pressure and temperature is essential to optimize the distillation process and prevent thermal degradation of heat-sensitive compounds.
Reflux Ratio
The reflux ratio, the ratio of condensed vapor returned to the distillation column to the amount collected as distillate, plays a crucial role in determining the purity and yield of the distillate.
Equipment Design
The design and quality of the distillation equipment, including the distillation column, condenser, and heating system, significantly impact the process efficiency and safety.
Safety Considerations
Distillation involves handling flammable and toxic solvents, necessitating strict safety measures. Proper ventilation, explosion-proof equipment, and regular monitoring of pressure and temperature are vital to ensure safe operation. Personal protective equipment (PPE) and emergency procedures must be in place to handle any accidental releases or equipment failures.
Role of Cold in Solvent Recovery Process
The application of cold in the solvent recovery process is crucial for enhancing efficiency and purity. Cooling plays a vital role in the condensation step, where the vaporized solvents are converted back into liquid form. Effective cooling ensures that the condensation occurs rapidly and efficiently, which is essential for high-purity distillation.
Condensers and Cooling Systems
In the solvent distillation system, condensers are designed to maximize the heat transfer from the vapor to the cooling medium, often water or air. The choice of cooling medium and the efficiency of the condenser directly impact the overall performance of the distillation unit. High-efficiency condensers can significantly reduce the energy required for cooling, contributing to energy savings and sustainability.
Temperature Control
Maintaining the correct temperature throughout the distillation process is critical for optimal separation. Overheating can lead to the decomposition of sensitive compounds, while insufficient cooling can result in incomplete condensation and reduced purity of the distillate. Advanced cooling systems with precise temperature control can help maintain the ideal conditions for each specific distillation task, ensuring the highest quality and yield.
Energy Efficiency
Modern solvent distillation systems incorporate energy-efficient cooling technologies to minimize energy consumption and environmental impact. By optimizing the cooling process, these systems can achieve significant energy savings, making them more cost-effective and environmentally friendly.
Where Used
Solvent distillation is employed in a wide range of industries:
Pharmaceutical Industry
In the pharmaceutical industry, solvent distillation is used to purify active pharmaceutical ingredients (APIs), recover solvents for reuse, and ensure the purity of final products.
Petrochemical Industry
The petrochemical industry relies on fractional and vacuum distillation to separate and refine crude oil into various valuable products, such as fuels, lubricants, and chemical feedstocks.
Chemical Manufacturing
Chemical manufacturing plants use distillation to separate and purify chemical compounds, ensuring the desired quality and consistency of their products.
Environmental and Waste Management
In environmental and waste management, solvent distillation systems are employed to recycle solvents from industrial waste streams, reducing waste and minimizing environmental impact.
Food and Beverage Industry
The food and beverage industry uses steam distillation to extract essential oils, flavors, and fragrances from natural sources, ensuring high-quality and pure products.
Conclusion
The solvent distillation process is a fundamental technique in various industries, enabling the separation and purification of chemical compounds based on their volatility. From simple distillation to more complex methods like azeotropic distillation, each type of distillation requires specialized equipment and careful control of operational parameters. Mirai’s advanced technologies offer efficient and safe solutions for solvent distillation, enhancing the performance and sustainability of industrial operations. By understanding the factors affecting distillation, implementing appropriate safety measures, and optimizing the role of cold in the process, industries can achieve high purity and yield, ensuring the quality and efficiency of their processes.